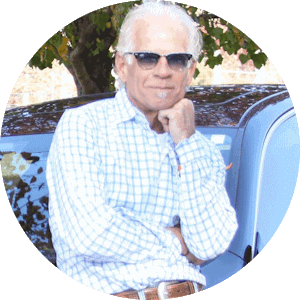
Pat Carden
CEO
It's All In the Digitizing
Digitizing is the term we use to describe the process of creating an embroidery pattern that interprets an image and converts it into stitches that can be used by a computerized embroidery machine to create an image from thread. Back in the 1980’s before computers, digitizers "punched" designs into a paper tape. The paper tape ran through the embroidery machine and was used to signal the needle and type of stitch to sew.
1980s Era Computer Digitizing Tape
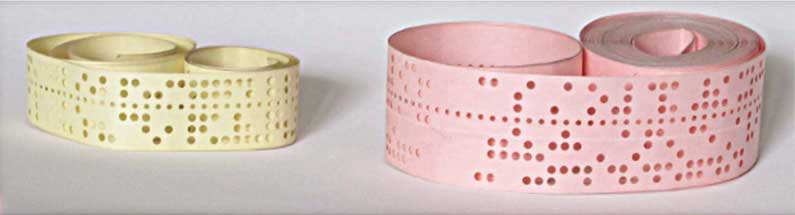
With the advent of the personal computer in the middle 80’s, digitizers switched to computer software to create the design and floppy disks were used to load the designs in the embroidery machine. Fast forward to the current era and all our embroidery machines are networked so we just download the pattern directly to the machine from our central repository of designs on our server.
Digitizing software has come a long ways too. Today modern digitizing software can import a vector file and create a embroidery pattern automatically but in most cases the output leaves a lot to be desired. If the digitizer didn’t learn the process by doing it the old, manual way, she may not have the experience necessary to fine tune the pattern to produce the optimal embroidery pattern.
Although we use the latest Wilcom embroidery software, our art department has decades of experience and we create our designs from scratch. The embroidery design controls not only the number of stitches and the colors but also the "underlay" which creates a stable base and the density of the stitches which produces a nice "thick" look if done properly.
The underlay needed and the density of the stitches is determined partly by the substrate onto which the embroidery is sewn. Lightweight and/or stretchy materials require more underlay and more thread density. Each design we produce is specifically digitized for a particularly item and fabric, so the design we created for a bag will probably need to be modified to work on a knit shirt. If you used our design for a shirt and tried to sew it on a hat, it would be a disaster.
The process is somewhat of an art and each time we create a new design, we send it to our sample machines to run a proof. After the design is run, we tweak it as necessary to make sure it meets our standards for world-class embroidery.
If you’ve ever seen an embroidery that looked "thin" and not very well aligned, it’s probably been generated automatically by an inexperienced digitizer. Automatic digitizing is definitely quick and efficient but the results can be less than optimal. That’s why we manually create each embroidery design that’s produced in our shop and why we proof it and refine it until we’re happy it meets our "world-class embroidery" standards.
Any embroidery is no better than the design used to create it which is no better than the digitizer who produced it.